Wir sind für Sie vor Ort!
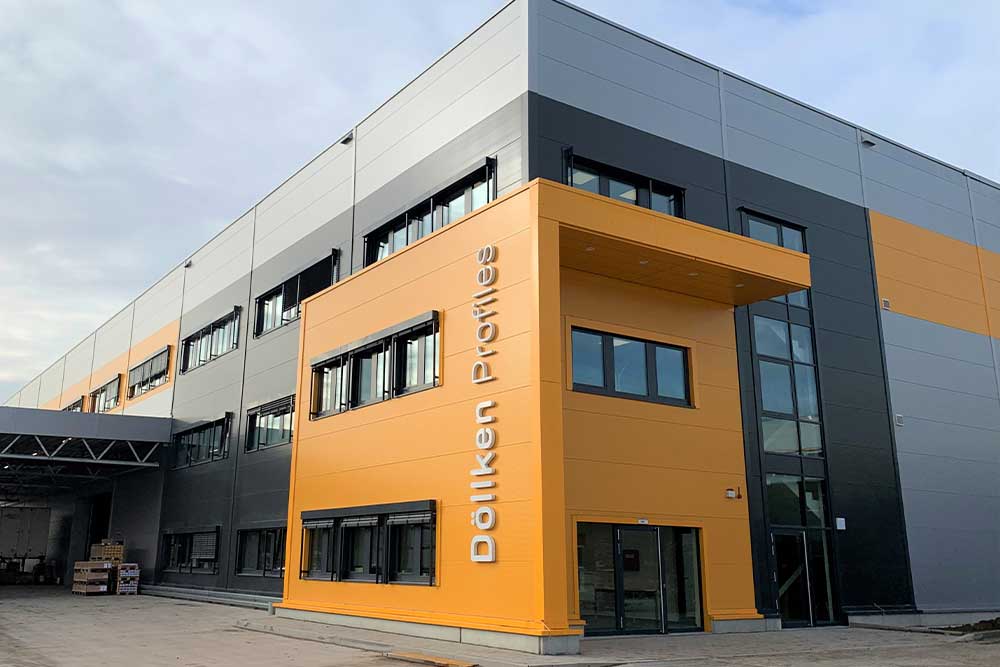
Hauptsitz Bönen
Der Standort Bönen wird von der Döllken Profiles GmbH und ihren Kunden als Ursprung und Heimat der erfolgreichen Kernsockelleisten angesehen. Seit über 50 Jahren, nämlich seit 1972, werden diese Art der Leisten, zu Beginn noch von der Schock & Co. GmbH, am Standort weiterentwickelt und produziert.
Die Aktivitäten der Döllken Profiles in Gladbeck wurden im Zuge der Zusammenlegung von Logistik und Verwaltung 2020 komplett nach Bönen umgezogen. Seit Anfang 2021 hat Döllken Profiles den Betrieb im erweiterten Stammwerk in Bönen erfolgreich aufgenommen und die alte bzw. neue Heimat bezogen.
Auf 10.000 m² zusätzlicher Fläche wurde im Werk Bönen nicht nur die Logistik auf ein völlig neues Niveau gebracht, sondern auch auf freiwerdenden Flächen zehn neue Produktionslinien installiert. Die Mitarbeiter im Werk Bönen produzieren hier unsere bewährten Klassiker wie Kernsockelleisten und technische Profile sowie innovative Produkte für Döllken Lighting.
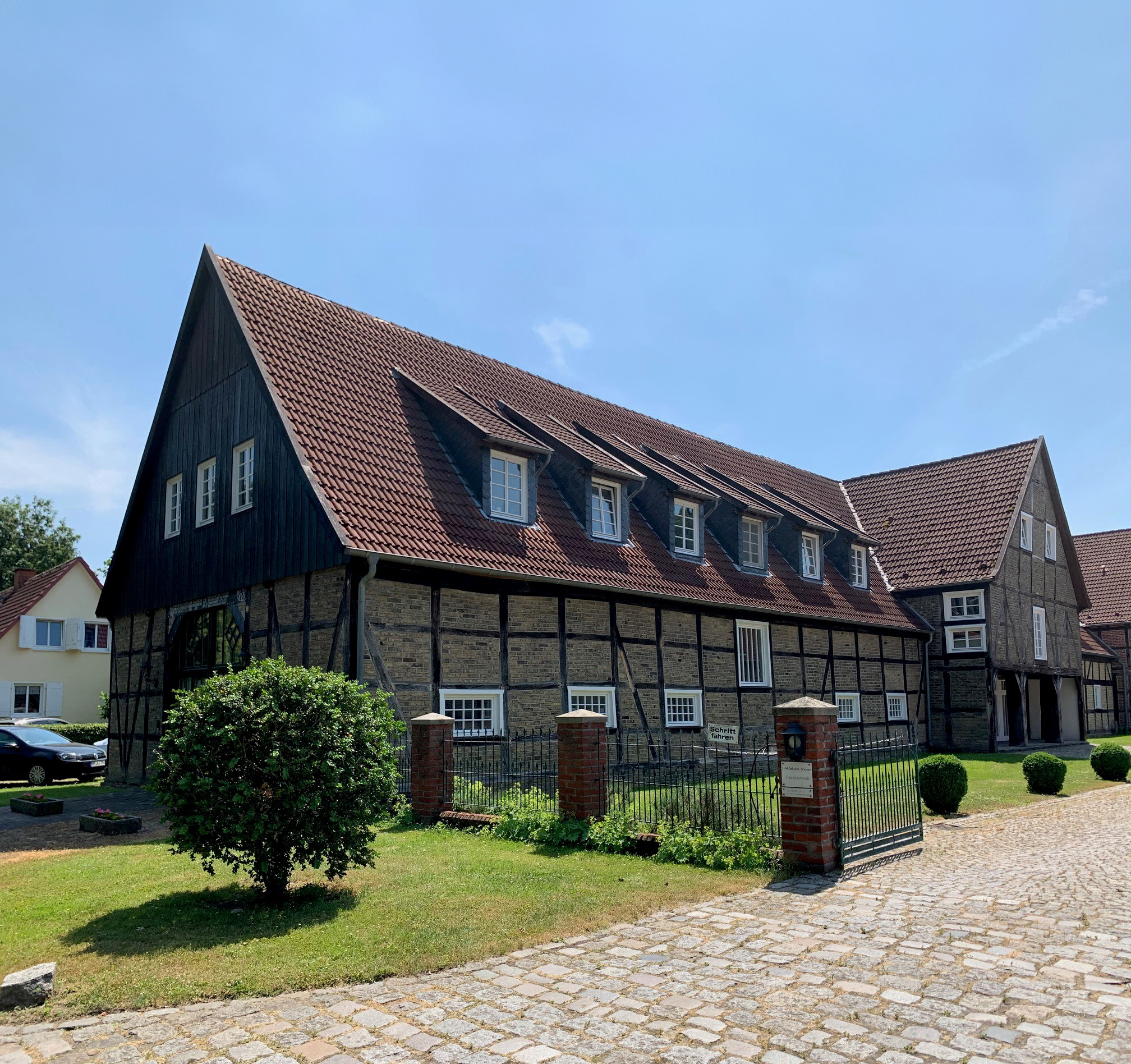
Unser Eventcenter in Hamm
In unmittelbarer Nähe zu unserem Hauptsitz in Bönen befindet sich das Döllken Profiles Eventcenter. Das Objekt fasst über 300 m² und ist Teil eines alten Gutshofs. Wir haben uns als Ziel gesetzt, langfristige Kundenbeziehungen zu verbessern und durch den persönlichen Kundenkontakt ein stärkeres Bewusstsein für unser Unternehmen und unsere Produkte zu schaffen. Mit unseren Kunden- und Handwerkerveranstaltungen bieten wir Ihnen ein umfangreiches Rund-um-Erlebnis mit Schulung, Rahmenprogramm und Betriebsführung an. Erfahren Sie interessante Tipps und Tricks rund um die Döllken Profiles Sockelleiste und Verlegung. Wir haben für unsere Kunden ein Schulungskonzept entwickelt, bei dem keine Fragen offen bleiben. Sockelleisten kleben oder nageln? Wie gehe ich mit einer ungeraden Wand um? Welche neuen Produkte gibt es? Diese und viele weitere Themen werden vor Ort mit unseren Anwendungstechnikern bearbeitet.
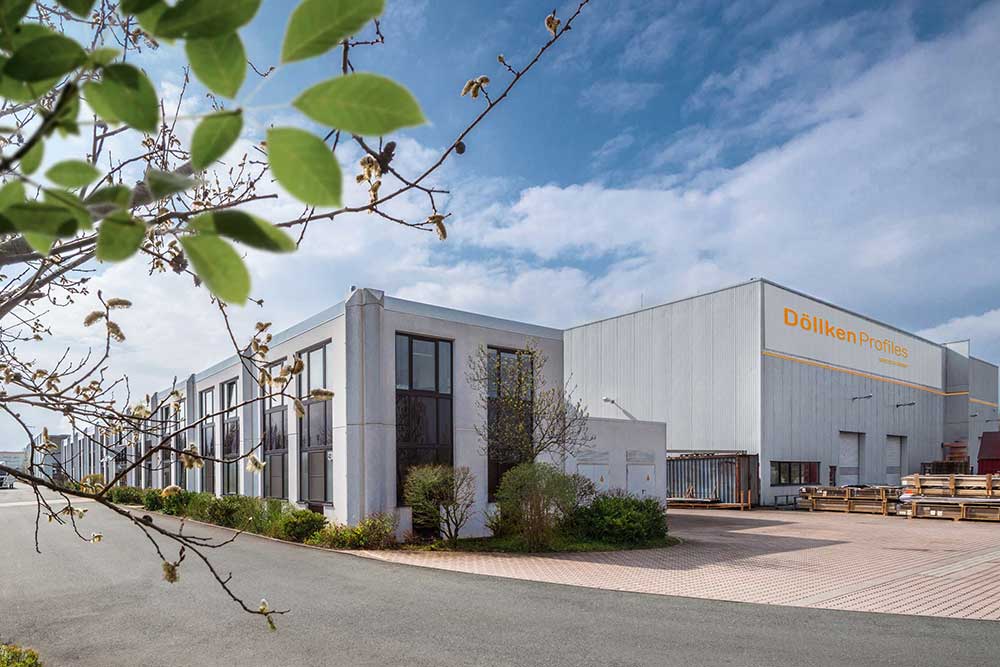
Werk Grammetal
Im thüringischen Grammetal werden seit 1991 Sockelleisten und andere Kunststoffprofile extrudiert. Döllken übernahm die Kunststoff GmbH Weimar,
die nach der Wiedervereinigung aus dem VEB Ausbau hervorging und bündelte hier die Tätigkeiten im Bereich Sockelleisten. 1998 zog die Döllken Weimar GmbH in den Neubau im Gewerbegebiet U.N.O. und richtete dort den Hauptsitz der Gesellschaft ein. Begonnen wurde damals mit 12 Extrusionslinien und etwa 70 Mitarbeitern. Aktuell werden in dem Werk mehrere Tausend Kilometer Kunststoffprofile pro Jahr hergestellt. Der Fertigungsschwerpunkt liegt in den Bereichen Hart-, Weich-, und Schaumextrusion.
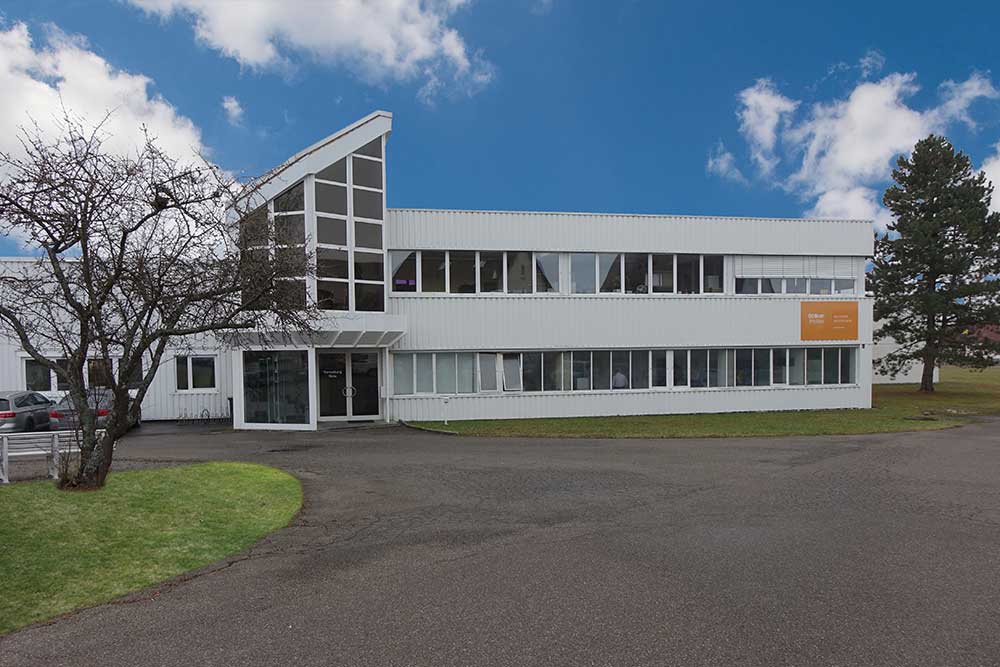
Werk Dunningen
In Dunningen, am Rande des Schwarzwaldes gelegen, produziert der Standort ausschließlich kundenspezifische Profile für die unterschiedlichsten Industriezweige, sowie Rollladensysteme für die Büromöbelindustrie. Die Kompetenzschwerpunkte unseres Standortes in Dunningen liegen in der individuellen Fertigungstechnik, Materialauswahl und Konfektion, um die jeweiligen Kundenanforderungen vollumfänglich abbilden zu können. So konnte im Laufe der Jahre ein breitgefächerter Kundenstamm in den Segmenten Bauindustrie, Elektrotechnik, Nutzfahrzeugbau, Klimatechnik und gewerbliche Kühlmöbel aufgebaut werden. Kunden schätzen unsere Flexibilität, Kundennähe, schnelle Projektumsetzungszeiten und konstante Qualität.
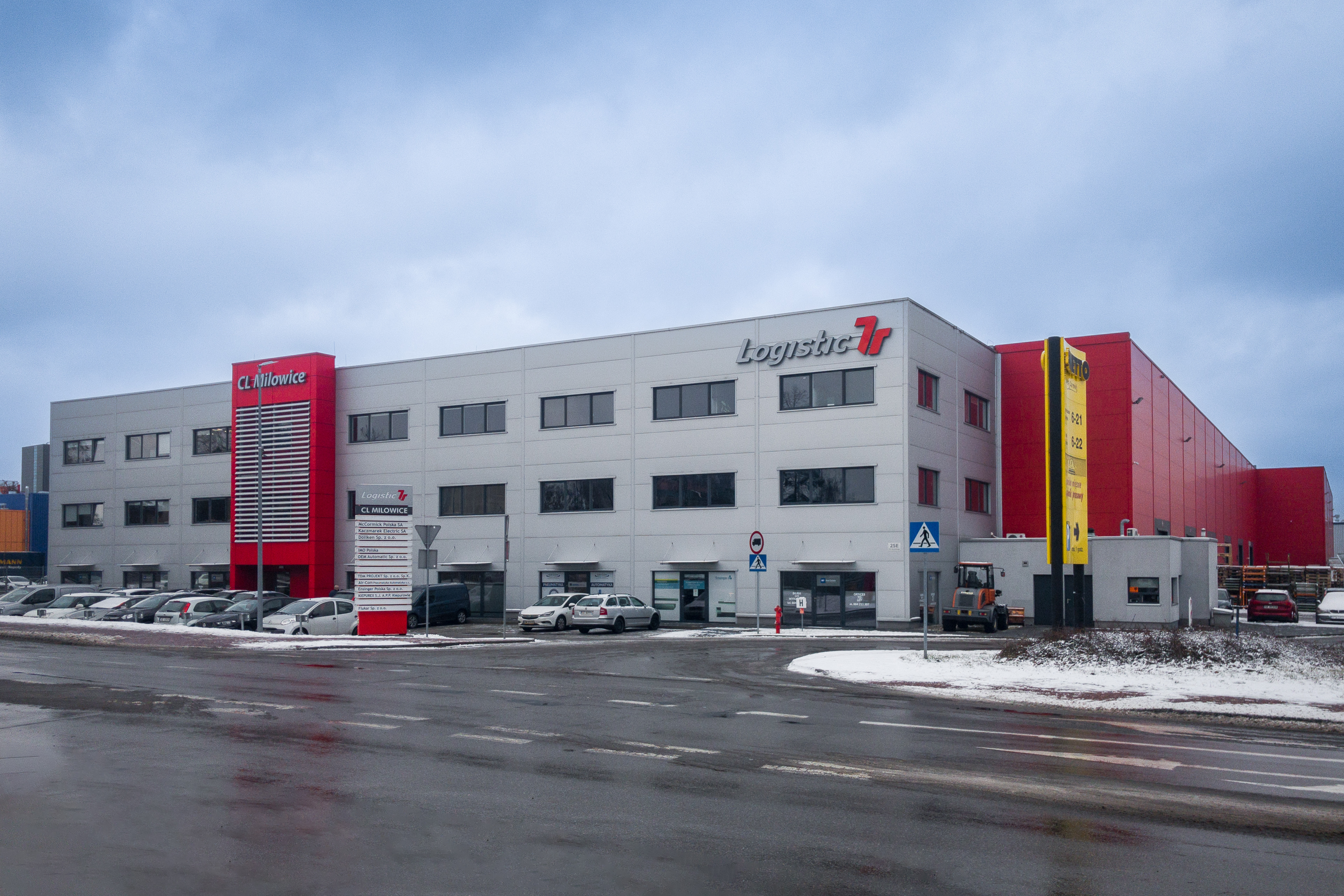
Standort Polen
Die polnische Niederlassung wurde im Jahre 1997 unter dem Namen Döllken & Praktikus Sp. z.o.o. gegründet. Der aktuelle Standort befindet sich in einem modernen Logistikzentrum in Sosnowiec und umfasst eine Bürofläche von 430 m² und Lagerfläche von 1800 m². Neben Döllken Produkten werden MDF-Profile, Aluminiumprofile, Massivholz und Laminatunterlagen angeboten. Aus unserem Lager für Ost- und Südeuropa beliefern wir fast 20 Länder, u. a. Albanien, Armenien, Bulgarien, Bosnien und Herzegowina, Estland, Griechenland, Kasachstan, Kosovo, Litauen, Lettland, Mazedonien, Mongolei, Montenegro, Rumänien, Serbien, Tschechien, Ukraine, Ungarn und Usbekistan.
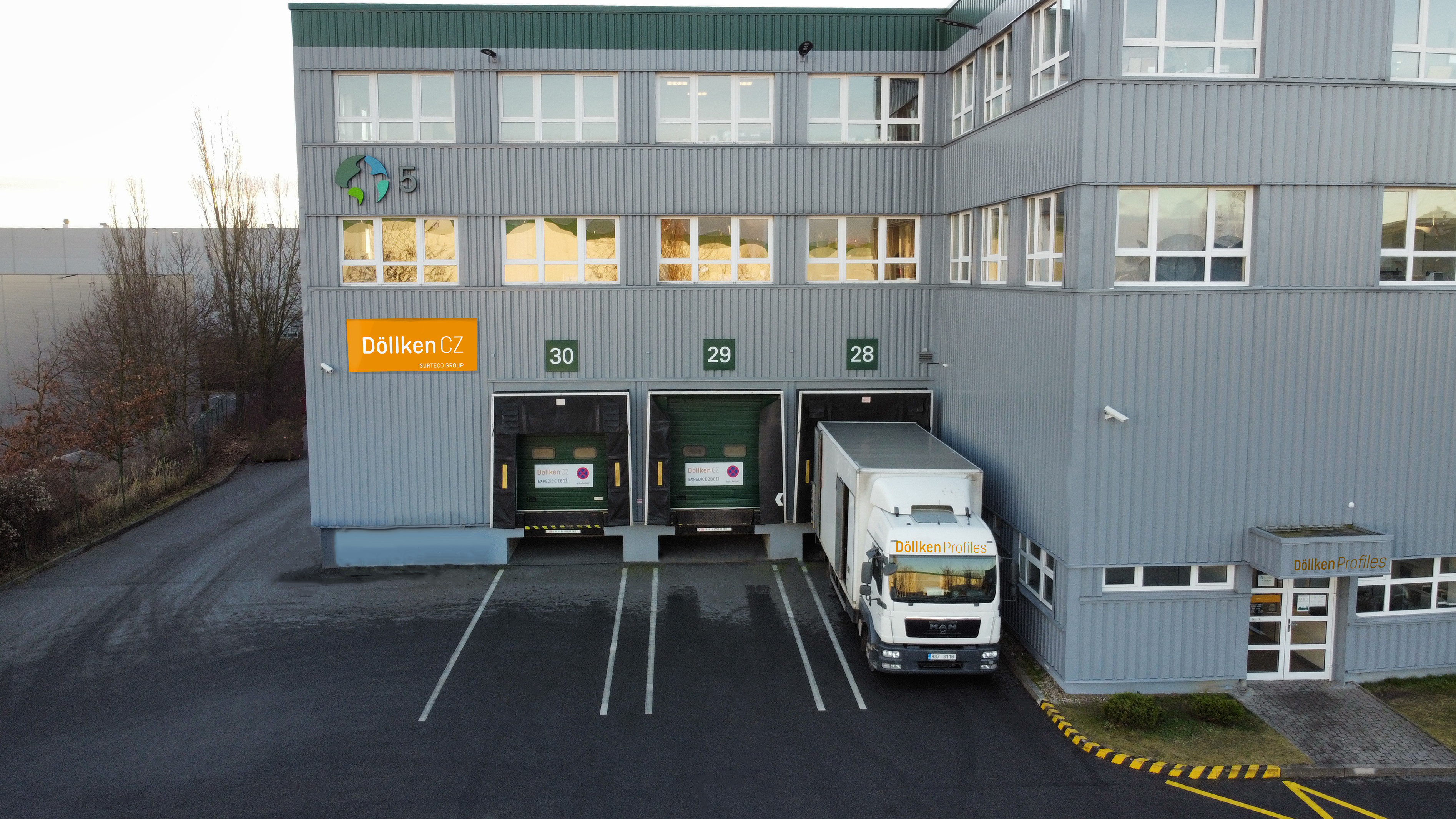
Standort Tschechien
Die Firma Döllken CZ s.r.o. ist seit mehr als 30 Jahren erfolgreich auf den Märkten in Tschechien und der Slowakei tätig und hat sich in dieser
Zeit als verlässlicher Partner für qualitativ hochwertige Produkte etabliert. In den letzten Jahren konnte das Unternehmen seine Marktpräsenz
weiter ausbauen und ist mittlerweile auch in Slowenien und Kroatien aktiv. In Rudná u Prahy befinden sich moderne Büroflächen als auch eine
große Lagerfläche. Diese Infrastruktur erlaubt es Döllken, flexibel und schnell auf die Anforderungen seiner Kunden zu reagieren. Dank des firmeneigenen Lagers können nicht nur kurze Lieferzeiten gewährleistet werden, sondern auch eine effiziente und übersichtliche Lagerhaltung, die optimal auf die Bedürfnisse des Marktes abgestimmt ist.
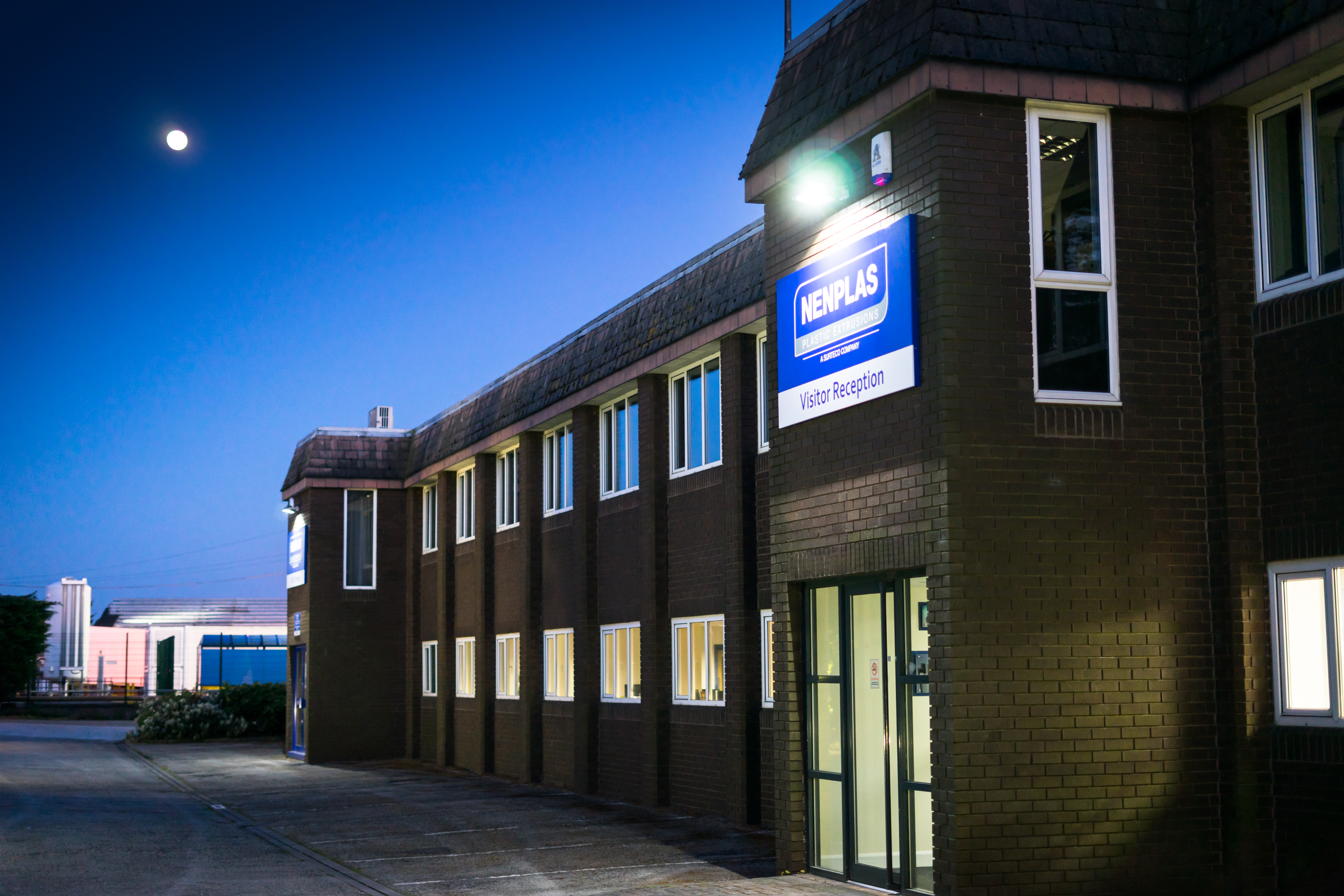
Standort Ashbourne
Nenplas Limited ist mit drei Produktionsstandorten ein führender Anbieter für Kunststoffextrusion in Großbritannien. Das Unternehmen betreibt insgesamt eine Vielzahl an Produktionslinien in Ashbourne, Stourport-on-Severn und Kettering. Die Kernkompetenzen umfassen Kunststoffextrusion, Inhouse-Materialcompounding, Werkzeugherstellung, Sekundärprozesse sowie ein umfassendes Logistiknetzwerk. Nenplas bedient Branchen wie Caravan- und Modulbau, Bauwesen, Elektronik und Transport. Der Fokus liegt auf flexiblen, maßgeschneiderten Lösungen und höchsten Qualitätsstandards. So unterstützt Nenplas ebenfalls seine Kunden bei der Optimierung ihrer Produkte.
Standort Stourport-on-Severn
Polyplas Extrusions Limited wurde vor fast 30 Jahren von Graham und Helen Tidman gegründet und begann mit zwei Extrusionslinien. Heute befindet sich das Unternehmen in einer modernen, 2006 fertiggestellten Produktionsstätte. 2013 verkauften die Gründer das Unternehmen an die Nenplas-Gruppe, die seit 2016 Teil der börsennotierten Surteco SE ist. Polyplas bietet ein umfassendes Leistungspaket von Design und Werkzeugbau bis zur Auslieferung und erfüllt höchste Qualitätsstandards (BS EN ISO 9001:2015). Polyplas legt seinen Fokus auf maßgeschneiderte Kunststoffprofile, ergänzt durch Standardprofile wie Dichtungen und Winkel. Zu den Kunden zählen verschiedene Branchen, darunter Bauwesen, Elektronik, Freizeit, Transport und Medizintechnik.